Batteriezellen: Wie sich Tesla und VW von Asien lossagen
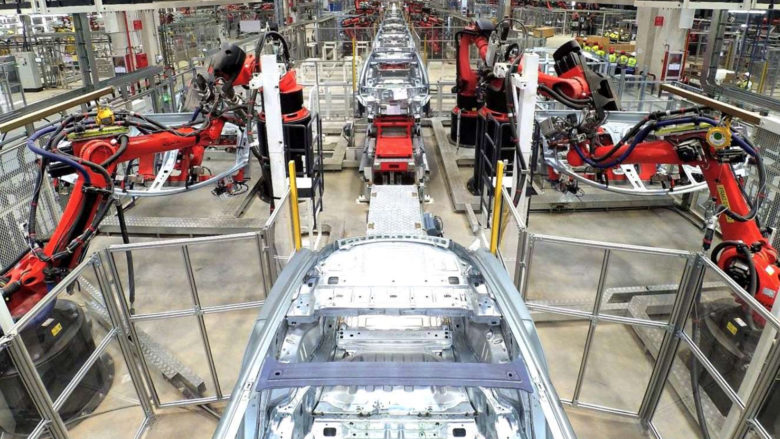
Früher haben sie unsere Gameboys, dann unsere Smartphones angetrieben – und jetzt bilden sie die Grundlage für die nächste Phase der Mobilität. Lithium-Ionen-Akkus sind neben der Software der essenzielle Baustein für Elektroautos, die langfristig Verbrenner ersetzen sollen. Doch gerade in Europa machen sich bereits erste Engpässe bemerkbar. Bei Autoherstellern wie Jaguar Land Rover, Audi oder Daimler läuft die Produktion von neuen Elektroautos nicht reibungslos – auch, weil die Batteriezellen in den benötigten Mengen nicht verfügbar sind.
Deswegen findet hinter den Kulissen ein Rennen um die Ressource Batterie statt. Bisher dominieren asiatische Produzenten den Markt – etwa Panasonic aus Japan, LG und Samsung aus Südkorea oder oder CATl und BYD aus China dominieren den Markt. Den Analysten von Oliver Wyman zufolge befinden sich 89 Prozent der Produktionskapazitäten für Lithium-Ionen-Akkus in Asien, nur drei Prozent in Europa. Das schmerzt. Mit der „European Battery Alliance“ (EBA) soll von der starken Abhängigkeit Europas von Asien entgegen gewirkt werden. Doch auch Elektroautohersteller Tesla, seit 2019 weltweiter Marktführer, will sich Branchenberichten von der Abhängigkeit von Panasonic lösen und künftig Batteriezellen selbst produzieren.
Prisma oder Kreis?
Akkus in Elektroautos sind folgendermaßen aufgebaut: Grundbestandteile sind Batteriezellen, die im Prinzip ähnlich funktionieren wie die Batterien, die man etwa in die Fernbedienung steckt. Diese werden dann in einem Batteriemodul gekoppelt, und mehrere dieser Module werden dann wiederum zu einem Batteriesystem zusammen gefügt. Derzeit gibt es in der Autobranche aber keinen Standard, sondern zwei verschiedene Zelltypen:
- Rundzelle: Dieser Zelltyp wird vor allem von asiatischen Herstellern produziert – sie sehen aus wie AA-Batterien, nur etwas größer. Tesla etwa hat pro Model S tausende Rundzellen mit einem Durchmesser von 18mm und einer Höhe von 65 Millimeter (kurz Typ 18650) verbaut, beim Model 3 kommen mittlerweile Zellen des Typs 21700 (21 mm im Durchmesser und 70 mm in der Höhe) zum Einsatz.
- Prismatische Zelle: Diese Zellen sind viel größer als Rundzellen und erinnern in Größe eher an einen Schuhkarton. In VWs kommenden ID.3 sind insgesamt bis zu 288 dieser Zellen verbaut (je 24 Zellen pro Modul), die zusammen ein komplettes Batteriesystem bilden
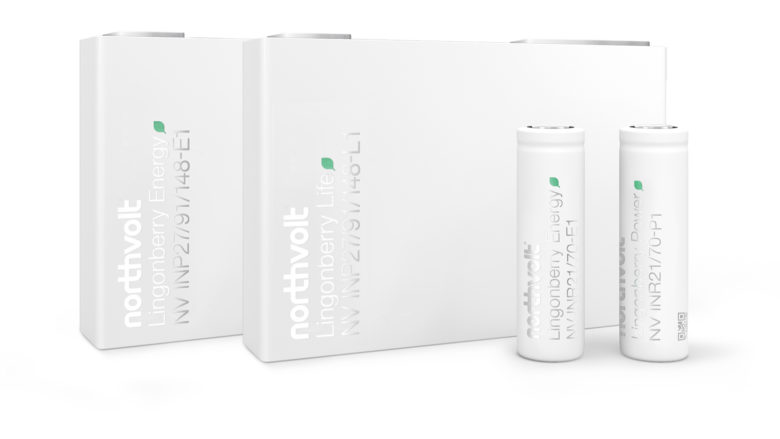
Welcher Zelltyp sich bei Elektroautos durchsetzen wird, ist noch nicht klar – derzeit will sich kaum eine Firma entweder für das eine oder das andere entscheiden. Volkswagen jedenfalls will sich in seiner Elektromobilitätsstrategie jedenfalls unabhängig von asiatischen Lieferanten machen und die Batteriezellen selbst in Europa produzieren. 2019 hat VW im Werk Salzgitter eine Pilotfertigung für Kleinserien eigener Batteriezellen gestartet und investiert Milliarden in den Bereich.
Northvolt und Maxwell
Außerdem soll mit Hilfe des Joint-Venture-Partners Northvolt aus Schweden dafür gesorgt werden, dass die Batteriezell-Produktion in Europa in großem Maßstab passieren kann. Auch BMW ist bei Northvolt investiert. Hier führt die Spur wieder unweigerlich zu Tesla – denn Northvolt wurde von zwei ehemaligen Tesla-Managern gestartet. Daimler wiederum baut ebenfalls seine eigenen Werke für Batterien.
Rund um Tesla, dass derzeit in enger Partnerschaft mit Panasonic die Batteriezellen fertigt, will Marktgerüchte zufolge das Ruder komplett selbst in die Hand nehmen. Im Werk Fremont soll derzeit offenbar eine Pilot-Fertigungslinie für eigene Batteriezellen aufbauen. Tesla hat in den letzten Jahren einige Firmen aufgekauft, die auf die Fertigung von Batteriezellen spezialisiert sind – und zwar Hibar Systems aus Kanada und Maxwell Technologies aus den USA. Letzteres Unternehmen hat sich Tesla satte 218 Millionen Dollar kosten lassen.
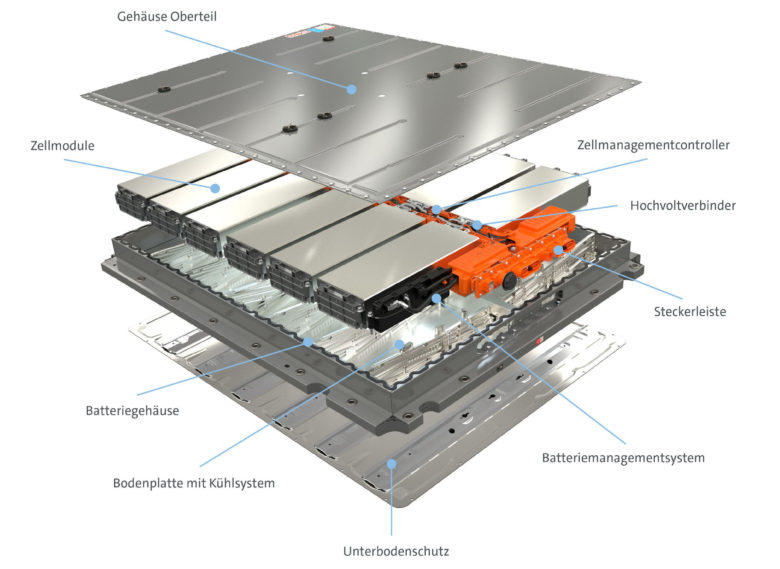