Level of industrial automation in Bulgaria: looking behind the numbers
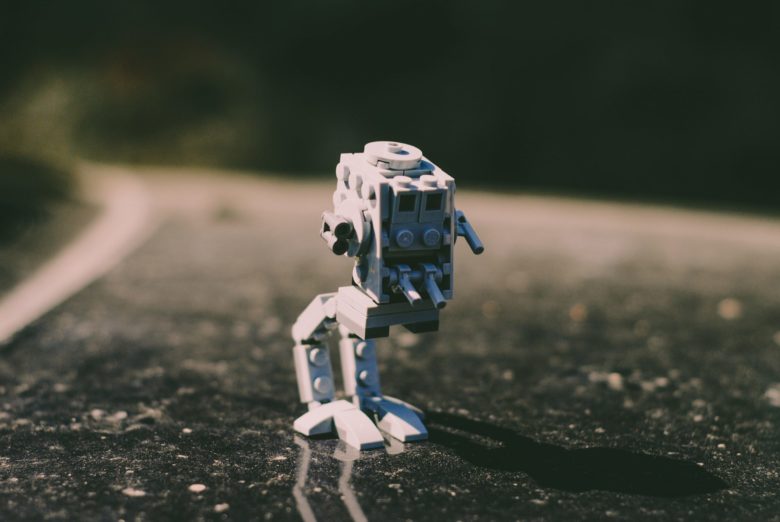
Industry 4.0 is no longer a new term. The digital transformation and automation of industry is at full swing and is the topic of multiple discussions. In Bulgaria too, stakeholders – from politicians to industry leaders – talk about the potential of the sector, including through the implementation of AI, big data, and blockchain technologies. Still, few focus on the current progress and ways to unfold the sector’s huge potential in the country. So, how is the industry actually doing?
From zero to hero
In a recent report on manufacturing automation, John Bradford, Makino’s Turnkey and Automation Applications Team Manager, outlines five levels of automation – from no automation and full manual control at level 0 to full automation at level 5 that requires few highly skilled technicians to keep things running smoothly. The methodology behind setting the five levels of automation has been developed by manufacturing consultants of Harbour Results Inc:
Level 0 – no automation – highly dependent on manual control from people, with reactive short-term processes and manual-analog technology;
Level 1– operator assistance – people are needed for at-machine monitoring, with reactive long-term processes and manual-digital technology;
Level 2 – partial automation – people handle on-site monitoring, the processes are partially proactive and technology is functionally automated;
Level 3 – conditional automation – people do remote monitoring, the processes are proactive and the level of technology is at cross-functional automation;
Level 4 – High automation – people only handle emergency interventions, the processes are predictive there are fully automated cells in the production process;
Level 5 – Full automation – the people that are needed are limited and upskilled technicians, the processes are self-optimizing in real-time and the level of technology is AI-driven within a full value stream.
Most industrial enterprises in Bulgaria are currently at level 2 or 3. The last two annual reports on automation in Bulgaria published by the Professional Association of Robotics and Automation (PARA) even highlight several companies that have reached level 5. Although the COVID-19 pandemic had a negative impact on investments in automation (50% of companies surveyed for the 2020 report admitted they had to postpone or cancel investments in automation due to Covid-19), another 44% said their plans to invest in automation remained unchanged.
+++Bulgarian Robotics: Success Stories Despite COVID 19+++
From software to industry robots
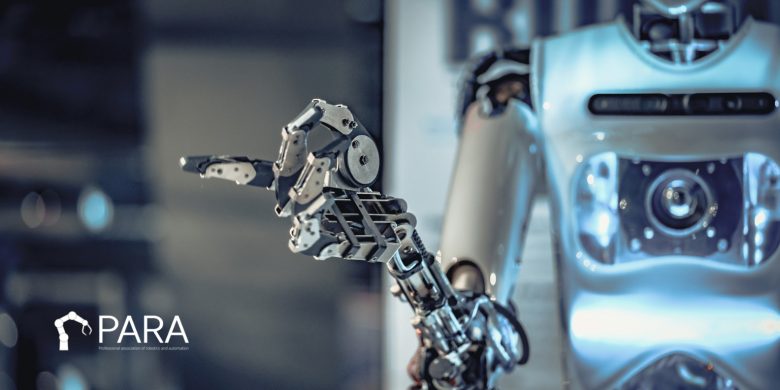
Plans for automation differ in the various sectors. For example, the automotive sector is leader in the implementation of industrial robotics, while companies that produce aluminum profiles or are in the furniture or dairy industries are mainly considering software automation. Whatever the automation solution maybe, Bulgarian manufacturing companies face similar barriers and enablers.
“The biggest barriers are mostly related to the required investment, the inflexible process of working with large vendors, and the fact that automation requires a level of training, infrastructure, and manufacturing digitalization that some companies lack,” Yonko Chuklev, co-founder of PARA, told Trending Topics SEE.
So far, the organization has held two consecutive annual surveys aimed at highlighting the biggest enablers of automation implementation in Bulgaria. Both of them showed that the leading driver behind these efforts is the need to increase production output. Other factors include the need to improve quality, replace human workforce amid labour market deficit, and efforts to increase safety.
Chuklev pointed out that subsidiaries of multinational companies and local manufacturers selling their goods on the global markets are the fastest adopters of industrial automation.
“On the one hand, when a multinational company starts manufacturing operations in Bulgaria, they implement the best practices from their global operations, which surely include automation technologies. On the other hand, local manufacturers with export operations are quick to implement automation innovations as well because they know that being competitive on the global market requires manufacturing capacity expansion, improved flexibility, product portfolio reengineering, which is all assisted by automation,” he explained.
From automation to digitalization – a tale about the chicken and the egg
In Industry 4.0, process automation and digitalization go hand to hand. Many people believe that digitalization comes after automation, but this is not always the case.
“The ‘Step 0’, as we call it, is the digitization and monitoring of the whole infrastructure – from the amount of paper used daily to energy consumption of the whole building or industry. By digitizing the business processes, we are also reviewing and improving them. It is a good exercise to do periodically in any organization – to streamline paperwork and find weak links or time leaks,” Kaloyan Georgiev, Solution Architect IoT, Automation and Energy Management, EcoStruxure Team Leader of Global Operations at Schneider Electric, told Trending Topics SEE.
“After ‘Step 0’, the good practice is to take ‘Step 1’, which is automation, based on digital data. Many companies start automating manual processes directly without revising and optimizing them. This results in higher integration costs and worse results,” the expert added.
According to him, digitalization of the Bulgarian industry has been a tough process for the past decade.
“The huge amount of aged hardware, low labor cost, and the lack of IT infrastructure have been the key factors slowing down this trend compared to other similar countries in Europe. Foreign investments and acquisitions on the other hand, together with local startups and knowledge, are the driving force supporting the transition to digital infrastructure. For the past couple of years, we have witnessed a major jump in adopting digitization, mainly in the monitoring of energy consumption or building automation,” Georgiev added.
Digital transformation in Bulgarian industry
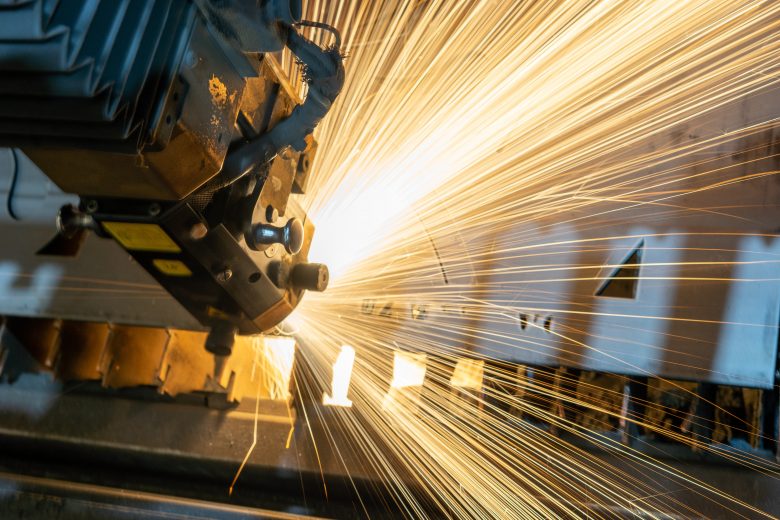
Georgiev estimates that between 40% and 60% of the Bulgarian industry has underwent some level of digital transformation.
“This is good in a way, because there is big room for improvement and good performance can still come from small investments in hardware or software. If we speak about the level of knowledge and the quality of digitization, I can proudly say that our industries are adopting the latest technological solutions available and also participating in the R&D or even inventing new ways for optimization and efficiency in the world scene,” he said.
Georgiev cited good examples such as Schneider Electric’s factory in Plovdiv which is one the smartest factories in the world, the smartest and most digital in the Balkans, and the first in Bulgaria with ISO50001 certificate for Energy Efficiency. “Other local companies such as Ataro Clima are also investing in almost fully automated and digital production which is bringing very good business and customer satisfaction results,” he said.
To boost the process of digital transformation of the manufacturing sector, Schneider Electric and PARA are organizing an open call for Bulgarian manufacturing companies that can apply to win free digitalization of their business in the contest “Start 4.0”. More information can be found here.
Such initiatives can help Bulgarian companies shorten the distance to the neighboring countries.
“Maybe compared to Romania or Greece, we are still a little bit behind in terms of the total rate of adoption of digital factories and digital production, but our growth rate is better compared to them,” Georgiev said. “We have seen how much added value the digitization of offices, homes, co-working spaces, and production can bring in touch times like 2020/2021 and many companies and industries have already made the difficult ‘Step 0’ in their digital journey. We also have very good technical competencies, experience, and field for improvement,” he added. According to him, within the next 3-5 years, the percentage of digitization, including business processes in Bulgaria, will go above 70%.